2000年以来,全球汽车工业得到了较快发展,中国是主要的增长力量。2000年至2015年,全球汽车产量从5837万辆增长至9068万辆,年均增速为2.98%;中国汽车产量从207万辆增至2450万辆,年均增速高达17.92%。而除中国以外的地区,汽车产量仅从2000年的5631万辆增长到2015年的6618万辆,年均增速仅为1.08%,可见在此期间,中国贡献了将近三分之二的增速。
1997-2015年全球和中国汽车产量情况
相关报告:智研咨询发布的《2017-2022年中国汽车轻量化市场运行态势及投资战略研究报告》
中国汽车制造业的迅猛发展使中国迅速成为全球的主要汽车市场。2015年,中国汽车年产量占全球的27%。但近几年,中国汽车产销量增速正在放缓。2015年产销量均在2450万辆左右,增速分别为3.3%、4.7%。根据中国汽车工业协会发布的《“十三五”中国汽车工业发展规划意见》,中国2020年汽车产销量将在2800~3000万辆,年均增速在2.7%~4.1%;国内品牌汽车市场占比50%以上,中国品牌新能源汽车销量达到100万辆。
汽车轻量化是在保证汽车安全性的前提条件下,对汽车产品进行优化设计,或者使用新材料在确保汽车综合性能指标的前提下,尽可能地降低汽车产品自身重量,达到减重、降耗、环保、安全的综合指标。在汽车上百年的制造历史当中,随着材料科学进步、社会发展等,汽车的设计、材料等都不断出现新变化。最初汽车出现时主要的制造材料是木材和钢铁;到了1920年以后,钢铁逐渐成为主要的制造材料;20世纪80年代末90年代初,第三次石油危机以后,以铝为代表的轻金属材料得到广泛应用。从材料方面来看,目前汽车整体上仍然以钢为主,但是随着铝合金、镁合金和各种复合材料等应用越发广泛。 根据美国环境保护部门的报告,我们发现汽车整备质量在20世纪80年代至21世纪初呈显著地增长趋势。这主要是因为汽车舒适化、自动化、智能化等趋势使汽车上各类电机、电子设备应用更为广泛,导致汽车整备质量有增长的趋势。进入21世纪以后,各国对温室气体排放、节能减排的要求也更加严格,开始倒逼车企进行轻量化的尝试。一方面通过各种轻量化的设计来,另一方面通过轻量化的材料的使用,都实现了汽车整备质量保持了相对稳定,设臵有所下降。
轿车重量与二氧化碳排放量
载重汽车重量与二氧化碳排放量
以车身轻量化系数来看,汽车轻量化是一种明显的趋势。通常,汽车车身、底盘(含悬架系统)、发动机三大件约占一辆汽车总重量的65%以上,其中车身内外覆盖件重量位居首位,大概占车重的四分之一至三分之一。所以车身的轻重广受重视,车身轻量化系数也是目前主要的评价汽车轻量化的指标。简单来说,就是以白车身重量作为分子,静态扭转刚度和车身脚印面积之积作为分母进行计算。根据学者计算的历年欧洲车身会议(ECB)展示的钢质轿车车身轻量化系数,可以发现总体上来说,车身轻量化系数还是朝着轻型化发展的。由于各年的参展车型、产品定位等不尽相同,造成了短期可比性差,但长期仍具有一定的可比性。
欧洲车身会议历年轿车车身轻量化系数变化趋势
汽车轻量化是节能减排、缓解资源环境压力的重要途径。据统计,目前我国汽车用汽、柴油消费量占全国汽柴油消费的比例已经达到55%左右,每年新增石油消费量的70%以上被新增汽车所消耗。进入21世纪以来,我国的石油消费量不断攀升,2000年至2014年间的平均增速达到了5.88%,进口量占表观消费量的比例从40.8%增至68.1%。过分依赖海外石油,这对我国的能源供应带来极大的风险,能源安全问题在我国愈显突出。
国内石油表观消费量及对外依存度
另外,石油消费快速增加也是我国碳排放总量迅速增加的重要原因之一。2015年全国的碳排放总量约为1990年时的4倍。我国资源、环境都承载着极大的压力。此外,尽管学者对于雾霾频发的原因有所争论,但对汽车尾气是重要的原因却有着较为一致的看法。 解决汽车节能减排问题一方面可以通过提高发动机效率,改善燃料经济性得以实现;另一方面就是通过汽车轻量化技术,在保障汽车安全性和其他基本性能不变的前提下,通过汽车减重来达到节能减排的效果。在提升发动机效率方面,实际上采用更为轻便的发动机制造材料也是重要的途径。目前,铸铝发动机的广泛运用就是一个例子。另外,汽车自身减重也能实现较好的节能减排效果。据研究表明,汽车燃料约60%消耗于汽车自重,汽油乘用车每减重100kg能节油0.39L/100km;若汽车整车重量降低10%,燃油消耗可降低6%~8%,排放降低5%~6%;而燃油消耗每减少1L,CO2排放量减少2.45kg。
汽车整备质量与百公里油耗关系
汽车整备质量与碳排放关系
汽车节能减排的巨大作用得到了政府的高度重视。政府一方面不断推行更高标准的汽车排放标准。特别是近些年来的排放标准更新速度明显加快,力度不断加大。从2007年全面推行国三到2014年全面推行国四标准用了将近7年时间,而国五标准于2015年底在珠三角实施汽车国五排放标准,东部11省市则在2016年4月起实施。国六标准则预计在2016年底制定,2017年在北京、上海等一线城市首先实行,预计2018年推广至全国。 另一方面政府对汽车规定了更为严格的油耗限值标准,这将直接推动汽车轻量化。根据相关法规政策,我国到2020年当年生产的乘用车平均燃料消耗量降至5.0升/百公里,2025年进一步下降至4升/百公里。相对日本和欧盟先进水平,我国的油耗限值仍有一定差距。据了解,日本和欧盟的燃料消耗限值更为严格,经过换算2015年日本平均油耗限值约为5.37升/百公里;欧盟地区则规定2020年新车平均排放应不高于95g/kg,换算成油耗为4升/百公里。
我国汽车油耗限值相关政策规定
可见,汽车的迅猛增加以及由此带来的资源消耗压力、环境保护压力导致汽车厂家不得不在传统汽车上使用更为轻质的材料,尽量降低汽车自重,提升燃料效率。特别是随着政府政策的执行落地,汽车轻量化进程将会得到更有力、更快速的推动。
轻量化对于汽车自身来说,一方面能够节油降耗,为车主带来经济效益,也能产生广泛的社会效益。以奥迪A8L为例,该车型是一款著名的轻量化材料应用汽车。其空间框架结构(ASF)包括22%的挤压成型铝合金件、35%的高精真空铸造铝件、35%的液压成型铝合金板材、8%的强化钢材44m无缝激光焊接和1847个冲钻铆接,白车身重量仅为241kg,比传统钢制结构车身重量降低40%。从节能降耗方面来看,一辆A8车行驶10万公里便可省油1200L,以6元/升计算便可节省汽油费用7200元。
另一方面轻量化也能够带来某些性能方面的提升,使车主具有更为舒适的驾驶体验。美国铝业协会提出,汽车每减重25%,就能够使汽车加速到96.56km/h的时间从原来的10s减少到6s;减轻汽车质量,同时可以降低动力和减少动力传动系统的负荷,能够使汽车在较低的牵引负荷状态下即可表现出同样的或者更好的性能。而一些轻量化材料的应用,除了减轻汽车自重外,还因为材料本身的特性能够给汽车带来一些性能上的改进。例如,使用铝、镁合金等轻质金属,可以使汽车震动减轻,从而使用更轻的反弹缓冲器;另外,在受到冲击时铝合金结构能吸收分散更多的能量,因而使汽车更安全、更舒适。
新能源汽车对于轻量化有着非常迫切的需求。通常新能源汽车由于电池模块能量密度小,导致同样功率的新能源汽车与传统燃油汽车相比要重15%以上。而续航里程是新能源汽车非常关键的指标。有研究表明,电动汽车整车质量每降低10%,续航里程就会增加5.5%左右。
车型 | 燃油款车重(kg) | 电动款车重(kg) | 电池容量(kWh) | 质量变化(kg) | 电池类型 | 续航里程(km) |
长安逸动 | 1330 | 1610 | 32 | 280 | 三元锂电 | 200 |
江淮iEV5 | 1100 | 1260 | 24 | 160 | 三元锂电 | 240 |
奇瑞eQ | 936 | 1128 | 22 | 192 | 三元锂电 | 200 |
北汽EV200 | 1091 | 1295 | 30 | 204 | 三元锂电 | 245 |
北汽EV160 | 1091 | 1295 | 25 | 204 | 磷酸铁锂 | 200 |
比亚迪E6 | 1610 | 2380 | 57 | 770 | 磷酸铁锂 | 300 |
因此相较传统燃油汽车,新能源车使用轻质化材料显得更为符合经济性。据了解,现在新能源车的电池箱、汽车板等各种部件都广泛采用了铝合金等轻量化材料。以特斯拉Model S为例,其电池组重达540公斤,占整车重量的26%。为减轻重量,特斯拉的车身外壳覆盖件全部采用铝合金制造,底盘也基本上采用铝合金,个别地方采用钛金属和高强度硼钢进行加强。正是各类轻量化材料的广泛应用,特斯拉Model S才能在电池组重量极大的条件的下,保持与相应燃油汽车差不多级别的整备质量。
轻量化的路径,一方面可以依靠合理的轻量化设计,去除一些不必要的重量;另一方面就是在保证安全性等原有性能基础上使用轻量化的材料,达到减轻自重的效果。这两方面实际上是相互促进的,新材料的使用需要新的设计,新设计带来新材料的应用。实践中的轻量化往往是依靠新材料的使用来实现的,新材料往往能够产生一次减重和二次优化减重两重效果。 从各种材料的减重效果来看,高强度钢、铝合金、镁合金、复合材料相对传统钢材的减重效果越发明显。复合材料(包括碳纤维和各类塑料)的减重效果最好,较传统钢材减重比例达到60%~70%;铝合金一般能够减轻30%~40%;高强度钢的密度与普通钢材差别不大,减重效果为15%左右。
类别 | 传统钢材 | 高强度钢 | 铝合金 | 复合材料 |
常见型号 | STAM540H | STAM735H | 6061-TB | EP-(CF+GF)70 |
拉伸强度/MPa | 540 | 735 | 365 | 400 |
比重 | 7.85 | 7.85 | 2.91 | 1.85 |
制件重量/kg | 20.2 | 17 | 13.7 | 6.2 |
减重效果/% | 0 | 15.80% | 32.20% | 69.30% |
从汽车主要材料变化轨迹来看,铸铁、中碳钢、高强度钢、轻质金属、复合材料等材料依次登场并发挥着重大作用。从1975 年至2012 年以来北美汽车使用材料比例来看,钢铁一直以来都是汽车用材的主流选择,现在的占比仍在50%以上,下滑幅度很小,但铸铁的用量则大幅降低了7 个百分点。另一方面,铝合金的使用量则大幅增加了7 个百分点。另外,塑料等其他材料的使用量也有所上升。专家预计,铝合金等轻质金属的使用是未来汽车轻量化的趋势,预计到2025 年,铝合金使用量占比能达到16%,塑料等材料的使用比例达到25%,钢的使用量将降低至46%。
1975 年北美汽车使用材料比例
2012 年北美汽车材料使用比例
具体地,整车各系统的轻量化思路各有侧重。从各板块占汽车整备质量比例来看, 车身、动力总成、底盘是最主要的重量构成,分别占汽车整备质量的28%、28%、27%,内饰及其他等占17%。因此,车身、动力总成和底盘也是轻量化的重点内容。车身方面,目前积极推广的还是以高强度钢替代普通碳钢为主,另外铝合金汽车板等也在逐步推广。底盘方面,结构件、安全件还是以钢材为主,但是铝合金、镁合金的应用也较为广泛。动力方面,一般是用铸铝发动机代替传统铸铁发动机,以及部分机械传动领域使用铝合金。内外饰则主要是以塑料等轻便材料进行替代。
整车各系统的轻量化思路
当前汽车轻量化材料的应用情况是,碳钢正在被高强度钢所取代,这是比较成熟的技术,目前正在广泛推行;另一方面,铝合金、镁合金的应用正在快速崛起,但总体渗透率不高;碳纤维等复合材料的使用则仅在高端领域得到了有限地应用。未来汽车轻量化材料里面,高强度钢、铝合金、镁合金与碳纤维都会根据自身的性价比在汽车上得到应用。
铝合金在汽车上的应用按照铝材加工类型分,主要可以分为铸造铝合金、变形铝合金。其中铸造铝合金用量大,约占汽车用铝量的80%,主要用于发动机缸体、缸盖、离合器壳、保险杠、车轮、发动机托架等。目前,国外许多汽车公司都采用了全铝型气缸体、气缸盖。另外,发达国家铝合金轮毂的使用率也已经达到了80%。 变形铝合金和铸造铝合金比,强度和韧性都有很大改善。变形铝合金的合金含量比较低,可以通过压力加工制成各类型材及成形零件,适用于强度要求高的结构件、疲劳件,例如车身面板、散热系统以及结构件和装饰件等。按照变形铝合金的合金类型分,主要可以分为2000系、5000系和6000系。目前,还有国家开发了7000系列,即铝镁锌铜合金,具有较高的硬度。
汽车用变形铝合金系列及其特点与应用范围
目前,铝合金在轮毂、散热器、油管、铸铝发动机等方面的应用非常广泛,但是在车身、覆盖件等方面的渗透率很低。根据咨询公司Ducker Worldwide的数据,铝合金板在汽车车身的渗透率2015年时仅为4%。尽管奥迪在1994年就制造了全铝车身的乘用车,并且在1999年首次将全铝车身汽车实现了量产。但铝汽车板、覆盖件的使用量仍旧较低。近两年,一是随着环保等压力加大,二是铝合金相关技术的成熟,汽车铝制ABS板的应用正在迅速推广。2015年,福特推出了新款的F150经典皮卡,其全部车身都采用了铝合金板。全部铝制车身的F150的问世,将会产生强大的示范效应,完善一系列与铝汽车板配套的产业链设施,推动汽车铝合金板的应用。
未来10 年铝合金在车身和覆盖件上的渗透率
镁合金在汽车轻量化应用中具有优异性能。一是质量密度小。镁合金的质量密度一般在2g/cm3 左右,比铝材轻36%,比锌合金轻73%,比钢轻77%。二是消震性能好。镁合金具有很高的阻尼容量和良好的消震性能,可承受较大的冲击振动,适于制造承受冲击载荷和振动的零部件,使汽车行驶更平稳、安全和舒适。三是比强度和比刚度高。相同质量的条件下,选用镁合金的构件具有更高的刚度。加入增强物的塑料,其刚度最多也只能达到镁合金的三分之一。四是铸造性能好。镁合金有良好的铸造性和尺寸稳定性,易加工,废品率低,从而可以降低生产成本。此外,镁与铁的亲和力小,固溶铁的能力低,不易粘模,铸模寿命比铝合金长2~3 倍。五是熔点低。镁合金的熔点和比热容较低,熔化时耗能较少,凝固速度快,动力学粘度低,铸造充型性好,使得压铸件生产周期短,易于成型薄壁结构件。六是回收利用性好。镁合金可以从废品、废料的再生资源中获得,并且可进行100%的回收利用, 镁在产品寿命周期的每一个阶段都有很高的利用价值。由于镁的熔点低,镁废料再生对能源要求也较低,镁的再生比塑料和铁等其它材料的再生需要少得多的能源用量。
中国汽车轻量化技术、材料等较国外落后。在汽车轻量化道路上,国外通常是先进零部件的开发者,引领轻量化材料的发展。国内汽车轻量化的水平与国际上相差较大。在高强度钢的渗透率方面,国内的自主品牌仅为40%~50%,而国外主流车型均在60%以上,而且高强度钢的屈服度还高于国内。在铝合金材料方面,国内汽车目前单车用铝量仅为100公斤左右,而全球的平均水平是170公斤,并且在汽车铝合金板等较为高端的产品上国内的生产技术和生产能力都较国外落后。镁合金材料方面,国内目前单车用镁量还不足1.5公斤,而欧洲单车用镁量在9.3~20.3公斤,北美单车镁合金用量在5.8~26.3公斤。国内受制于压铸技术、客户认证等各方面的原因镁的使用量远远低于国外。 中国汽车轻量化有广阔的市场空间。一方面,合资车型随着国外原型的引进通常会对国内的零部件厂商产生需求,这将有利于国内企业拓展轻量化材料业务。另一方面,广泛使用轻量化材料的合资车、进口车的进入对自主品牌车企来说也是一种很好的示范,从而带动国内轻量化材料市场发展。总体上来看,中国汽车轻量化市场前景相当广阔,相关企业将会受益于汽车轻量化。

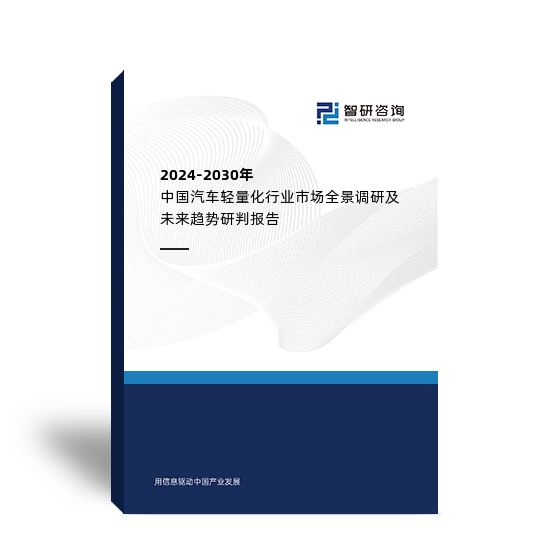
2025-2031年中国汽车轻量化行业市场全景调研及未来趋势研判报告
《2025-2031年中国汽车轻量化行业市场全景调研及未来趋势研判报告》共十三章,包含2025-2031年汽车轻量化行业发展趋势分析,2025-2031年汽车轻量化行业投资前景分析,市场指标预测及行业项目投资建议等内容。
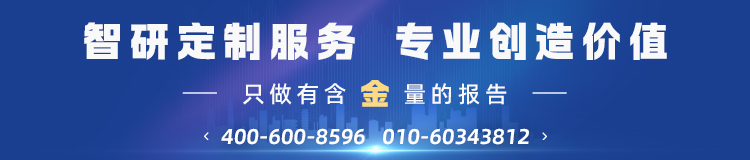
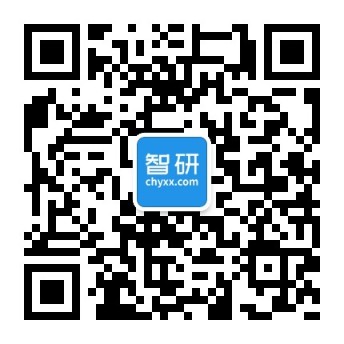
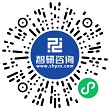
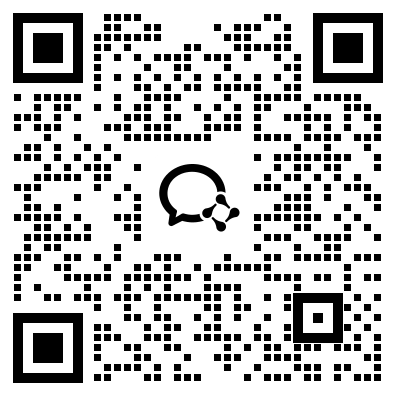