增材制造又称“3D 打印”,是以计算机三维设计模型为蓝本,通过软件分层离散和数控成型系统,利用激光束、热熔喷嘴等方式将金属粉末、陶瓷粉末、塑料、细胞组织等特殊材料进行逐层堆积黏结,最终叠加成型,制造出实体产品。与传统制造业通过模具、车铣等机械加工方式对原材料进行定型、切削以最终生产成品不同,3D 打印将三维实体变为若干个二维平面,通过对材料处理并逐层叠加进行生产,大大降低了制造的复杂度。这种数字化制造模式不需要复杂的工艺、不需要庞大的机床、不需要众多的人力,直接从计算机图形数据中便可生成任何形状的零件,使生产制造得以向更广的生产人群范围延伸。
一、发展历程
增材制造技术起源于美国。1940 年,Perera 提出了切割硬纸板并逐层粘结成三维地形图的方法,直到 20 世纪 80 年代末,3D 打印制造技术实现了根本性发展。1988年美国科学家 Hull 获得光固化技术的发明专利,并成立了全球首家增材制造公司3D Systems。21 世纪开始,随着工艺、材料和装备的日益成熟,增材制造技术的应用范围由模型和原型制造进入产品快速制造阶段,在航空航天等高端制造领域得到规模应用。
国外增材制造技术的发展历程
思想萌芽
|
技术 诞生
|
装备推出
|
大规模应用
|
增材制造技术的核心思想起源于美国。1940年,Perera提出了切割硬纸板并逐层粘结成三维地形图的方法。直到20世纪80年代末,3D打印制造技术实现了根本性发展,仅在1986至1998年注册的美国专利就多达24项。
|
1986年美国的Hull发明了光固化技术(SLA)。1988年Feygin发明了分层实体制造技术(LOM)。1989年Deckard发明了粉末激光烧结技术(SLS)。1992年Crump发明了熔融沉积制造技术(FDM)。1993年Sachs发明了喷头打印技术(3DP)。
|
1988年美国的3D Systems公司生产出了第一台增材制造装备SLA250,开创了增材制造技术发展的新纪元。1996年,3DSystems使用喷墨打印技术,制造出其第一台3DP装备Actua2100。同年,美国Zcorp公司也发布了Z402型3DP装备。
|
2002年,德国成功研制了选择性激光熔化增材制造装备(SLM),同时,电子束熔化(EBM)、激光工程净成形(LENS)等一系列新技术与装备涌现出来。这些技术解决一些传统制造工艺面临的难加工甚至是无法加工等制造难题。
|
数据来源:公开资料整理
二、现状
1、应用
国内高校和企业通过科研开发和设备产业化改变了增材制造设备早期仰赖进口的局面。我国也逐渐建立起 20 多个增材制造设备服务中心,设备用户遍布医疗、航空航天、汽车、军工等行业。但是增材制造技术仍处于发展之中,其成熟度还远不如金属切削、铸、锻、焊、粉末冶金等制造技术。
增材制造技术是综合多学科的新技术,其在大型复杂构件和高价值材料产品等制造中具有成本、效率、质量诸多优势。
缩短研发周期:制造速度快,成形后的近形件仅需少量后续机加工,可以显著缩短零部件的生产周期,满足快速响应要求。
复杂结构得以实现 :能轻松实现复杂结构件的制造,同时还能实现单一零件中材料成分的实时连续变化,使零部件的不同部位具有不同的成分和性能,是制造异质材料的最佳工艺,大幅提升了设计和创新能力。
满足轻量化需求,减少应力集中 ,增加使用寿命 :优化复杂零部件的结构,在保证性能的前提下,将复杂结构经变换重新设计成简单结构,从而起到减轻重量的效果。而且通过优化零件结构,能使零件的应力呈现出最合理化的分布,减少疲劳裂纹产生的危险,从而增加使用寿命。
提升零部件的强度和耐用性 :金属增材制造技术能方便地加工高熔点、高硬度的高温合金、钛合金等难加工材料。金属零件直接成形时的快速凝固特征可提高零件的机械性能和耐腐蚀性能。
具有较高的设计自由度:可以构建出其它制造工艺所不能实现的形状,可以从纯粹考虑功能性的方面来设计部件,且无需考虑与制造相关的限制。
小批量生产的经济性高:无需生产或装配硬模具,且装夹过程用时较短,因此不存在需要通过大批量生产才能抵消的典型的生产成本。
提高材料利用率 :是净成形水平最高的工艺,其后续机加工所必须切削掉的材料数量是很微量的。
能减少装配次数:通过增材制造所构建的复杂形状可以一体成形,能省去投入到装配工序的工作量、需涉及的坚固件、钎焊或焊接工序,还节省了为装配操作而添加的多余表面形状和材料,大大提升了生产效率。
增材制造主要应用领域
应用领域
|
典型应用
|
航空发动机
|
机身结构件、发动机零件、燃油喷嘴等
|
航空航天
|
钛合金进气边、高温合金机匣、大型结构件整体等
|
汽车零件
|
汽车发动机、变速箱、泵、车身、底盘、压缩机等
|
医疗
|
齿科、骨科、医疗器械、医用教学、活体器官等
|
模具
|
液压膨胀夹头、外圆铰刀、冷却麻花钻头、整体式液压膨胀夹头
|
数据来源:公开资料整理
在国外,增材制造技术已经在火箭发动机喷嘴、飞机复杂结构件、航空发动机复杂构件等武器装备产品研制中获得应用,并且开始由研究开发阶段向工程化应用阶段迈进。金属三维打印材料的应用领域相当广泛,如石化工程、航空航天、汽车制造、注塑模具等。这项技术已被应用于多个行业领域,并且发挥着越来越重要的作用。
即使已经过较长时间的发展,增材制造技术还面临一些困难和挑战等待全世界的学者去克服。首先,增材制造技术的工业标准需要被系统建立。生产过程需要有清晰的指导和参数设置,以便使生产出的产品具有稳定的性能表现。其次,可用的材料和产品的尺寸需要被进一步扩大。这项困难在航空航天行业表现的尤为突出,因为它所使用的材料通常需要能够耐住极高温和极低温的考验。最后,对于增材制造技术产品的机械性能需要继续深入研究。即使对于增材制造技术所生产的产品的机械性能研究从未停止,但在疲劳性能、残余应力和断裂韧性方面还有较大的空白。
2、 产业链
增材制造打印产业链上游主要包括 3D 建模工具和原材料。其中,3D 建模工具包括 3D 建模软件、3D 建模扫描仪和 3D 模型数据平台。与此相对应,聚集在产业链上游企业包括三维软件开发商以及耗材生产商等。增材制造原材料主要包括金属增材制造材料、无机非金属增材制造材料、有机高分子增材制造材料以及生物增材制造材料等几类。
增材制造材料的类别和应用领域
类别
|
材料名称
|
应用领域
|
金属增材制造材料
|
钛合金、高温合金、铝合金等金属粉末、液态金属材料等
|
航天航空、船舶工业、核工业、汽车工业、轨道交通等高性能、难加工零部件与模具的直接制造
|
非金属增材制造材料
|
高性能陶瓷,非金属矿、宝玉石材料、树脂砂、覆沙膜、硅砂、硅酸盐类等
|
航天航空、汽车发动机等制造用模具开发及功能零部件制造;工业产品原型制造及创新创意产品生产
|
有机高分子增材制造材料
|
树脂类:光敏树脂;丝材类:PLA、ABS、PC、PPSF、PETG 等;粉末
|
工/模具制造、原型验证、科研教学、文物修复与保护、生物医疗等
|
生物增材制造材料
|
生物可降解材料、生物相容性材料、活细胞等
|
药物控制释放、器官移植、组织和软骨质结构再生与重建等
|
数据来源:公开资料整理
增材制造设备是牵动增材制造行业发展的关键之一。增材制造设备可分为桌面级打印机和工业打印机。近年来随着国外桌面级打印机相关专利保护到期,技术壁垒下降,国内桌面级打印机厂家数量急剧增长,新进企业增多,加大了国内桌面级增材制造市场的竞争程度。与桌面级打印机市场相比,工业级打印机技术壁垒高,资本投入大,一直以来发展较为缓慢,但当前工业级增材制造产业受到国家政策大力支持,整个市场目前已开始呈现快速增长形势。增材制造的核心专利大多被设备厂商掌握,因此在整个产业链中占据主导地位,这些设备生产厂商大多亦提供打印服务业务。近年来,增材制造行业整合加剧,通过并购增材制造打印软件公司、材料公司、服务提供商等,设备生产企业转变为综合方案提供商,加强了对产业链的整体掌控能力。
增材制造技术的下游应用以航空航天、军工、船舶工业、核工业、汽车工业、轨道交通及医疗为主。目前该技术在下游行业的应用方式主要分为直接制造、设计验证和原型制造。直接制造是根据三维模型,直接用增材制造技术生产最终产品,具有产品定制性强与产品精度/硬度高的特点,是未来增材制造技术的主要发展趋势。与传统制造相比,采用增材制造技术进行设计验证及原型制造可节约时间与经济成本。此外,增材制造在维修领域也具有市场,使用增材制造技术不仅能简化维修程序,还可实现传统工艺无法实现的高还原度与制造材料原型匹配的功能。
三、格局
全球增材制造产业已基本形成了美、欧等发达国家和地区主导,亚洲国家和地区后起追赶的发展态势。美国率先将增材制造产业上升到国家战略发展高度,引领技术创新和产业化。欧盟及成员国注重发展金属增材制造技术,产业发展和技术应用走在世界前列。俄罗斯凭借在激光领域的技术优势,积极发展激光增材制造技术研究和应用。日本全力振兴增材制造产业,借助增材制造技术重塑制造业国际竞争力。
1、国内高校
(1) 西北工业大学金属高性能增材制造重点实验室
金属高性能增材制造与创新设计工业和信息化部重点实验室于 2015 年获得工业和信息化部认定,是西北工业大学首批获得工业和信息化部认定的三个重点实验室之一。实验室以金属构件的高性能增材制造技术与结构功能一体化创新设计技术为研究对象,提升我国金属高性能增材制造技术及其相关自主创新能力,发展创新设计与金属高性能增材制造的科学原理和先进技术,培养大批具备增材制造新理念、新知识和新技能的设计师、工程师和管理者,推动金属高性能增材制造技术在航空、航天、航海、能源等行业的更广泛应用。
实验室现有支撑学科为材料科学与工程和航空宇航科学与技术两个一级学科国家重点学科,以及控制理论与控制工程和计算机应用技术两个二级学科国家重点学科。现任实验室主任为林鑫教授,学术委员会主任为中国工程院院士卢秉恒教授。实验室围绕两个研究方向,设置了 8 个研究团队,其中载能束增材制造团队的带头人黄卫东即是铂力特公司的董事、首席科学家。
(2)清华大学生物制造 与快速成形技术北京市重点实验室
生物制造与快速成形技术是机械工程与生物、医学及材料科学的新兴交叉领域。实验室自 1990 年代初开始进行快速原型技术的探索和开发,先后开发了分层实体制造(SSM)、熔融挤出制造(MEM)、无模铸型制造(PCM)、冷冻冰成形(FIC)、多功能快速成形系统(M-RPMS)。2000 年后,实验室开始了金属材料和生物材料及细胞的增材制造(3D 打印)技术研究,开发了电子束选区熔化制造(EBSM)、低温沉积制造(LDM)和三维细胞受控组装(3DCCA)等增材制造和生物三维打印技术与装备。
2014 年实验室在世界上首次用三维打印方式构建出体外三维肿瘤模型,BBC 也为此进行了采访,并做了特别报道。此外,实验室还在异质多细胞打印、细胞芯片3D 打印制造、体外生命系统构建、电子束复合增材制造、增材制造多尺度多物理场计算模拟等前沿领域进行了开拓和探索。近年来,实验室获得了 2011 年“863”生物和医药技术领域重点项目课题、2012 年自然科学基金重点项目、2017 年科技部“增材制造与激光制造”重点研发计划等重要项目。2016 年实验室被教育部批准成为“111 计划”生物制造与体外生命系统工程交叉学科创新引智基地,进一步促进了实验室与世界各国优秀学者的交流,促进实验室国际学术地位保持和提升。实验室获得过北京市科技进步一等奖和国家科技进步二等奖。
(3)北京航空航天大学 “大型整体金属构件激光直接制造”研究中心
研究中心以王华明院士为核心,依托大型金属构件增材制造“国家工程实验室”和激光增材制造“国防科技工业研究应用中心”,从事钛、钢、镍、铝等高性能难加工合金构件增材制造及关键运动副零部件激光表面工程技术的基础、应用基础和工程化应用关键技术研究,主要集中于大型复杂金属结构件的制造,为中国航空航天的快速发展提供强有力的支持。研究中心已承担包括国防 973、国家自然科学基金、863 等重要科研项目 30 余项,发表 SCI 收录论文 200 余篇,获得国家发明专利授权 10 余项,获国防科学技术一等奖 2 项、国家技术发明一等奖 1 项。
2、国内科研单位
(1)中航工业航空制造技术研究院
中国航空制造技术研究院隶属于中国航空工业集团公司,是专门从事航空与国防先进制造技术研究与专用装备开发的综合性研究机构,是 2016 年 12 月以北京航空制造工程研究所(625 所)为基础,整合中航工业基础院相关单位和业务组建而成。制造院以 625 所为院本部,下设 2 家研究所(北京航空精密机械研究所、济南特种结构研究所)和 1 家上市公司(中航航空高科技股份有限公司),拥有 1个国家级重点实验室、1 个国家级创新中心、1 个国家级国际科技合作基地、3 个北京市重点实验室、1 个北京市工程技术研究中心、1 个北京市国际科技合作基地、6 个集团重点实验室(其中之一为增材制造航空科技重点实验室)、4 个集团技术(研发、创新)中心。
制造院主要承担航空材料、制造工艺、专用装备等基础、应用和工程转化研究工作,为我国新型飞机、发动机、导弹等航空装备研制和航空工厂的技术改造提供了大量先进制造技术和工艺装备。同时,制造院也为国防工业其它领域,如航天、电子、兵器、船舶等提供了先进制造技术。制造院先后与美国、俄罗斯、德国、法国、瑞士、意大利、日本等 30 多个国家和地区的研究机构、企业建立了长期的技术交流和经济合作关系。
(2)南京增材制造研究院
“南京增材制造(3D 打印)研究院” 成立于 2013 年 12 月 8 日,是在江苏省政府领导下,由南京市江宁区政府与卢秉恒院士共同发起创建的一个专门从事“3D打印技术、装备及应用”的科研和成果转化机构。中国工程院院士、西安交通大学卢秉恒教授担任“南京增材制造研究院”院长,研发团队包括专职研发队伍 80 余人,来自国内著名高校的在读博士和硕士研究生40 余人,同时聘请了国内外著名高校、研究单位和知名企业的专家、教授和艺术家 30 余人担任技术顾问、导师或兼职研发人员。
3、国内外企业
(1)德国 EOS
德国 EOS 成立于 1989 年,是金属和高分子材料工业 3D 打印的领导者。EOS 公司现在已经成为全球最大的金属增材制造设备提供商,覆盖产品开发、材料、设备、工艺和咨询服务等一整套体系,年产能可达 1000 台工业级 3D 打印机。公司在全球拥有超过 2000 家客户,分布在 65 个不同国家。截止 2017 年底,EOS 全球装机量已经超过 3000 台,在中国的总装机量已经超过 300 台,也是中国装机量最大的供应商。2017 年公司 3D 打印设备(可能包含材料、软件等)销售收入 2.4 亿美元(按照美元兑人民币汇率 6.87 计算,约合人民币 16.49 亿元)。
(2) 美国 3D Systems
3D Systems 成立于 1986 年,是全球销售规模最大的 3D 打印解决方案供应商,提供“从设计到制造”全套增材制造解决方案,包括 3D 打印机、打印材料、打印服务和云计算按需定制部件。公司主要技术路线包括材料挤出、激光烧结、光固化成形及 3DP 等,可选材料包括塑料、金属、陶瓷等。2018 年公司实现营业收入 6.88亿美元((按照美元兑人民币汇率 6.87 计算,约合人民币 47.27 亿元),同比增长6.44%,归母净利润-4551 万美元。
(3)美国通用电气公司
与 3D Systems、Stratasys 等随 3D 打印一同兴起的增材制造巨头不同,GE(通用电气)诞生于第二次工业革命期间,在 3D 打印出现之前早已成为工业巨擘,是传统工业企业入局 3D 打印市场取得巨大成功的杰出代表。GE 通过全球并购实现了从增材制造应用向增材制造装备及服务供应商转变。2016 年,GE 公司成功收购瑞典 Arcam 公司和德国 Concept Laser 公司,成为金属增材制造领域的佼佼者,并在航空发动机领域实现了增材制造零部件的规模化应用。除了成立 GE Additive主攻增材制造之外,GE 的其他部门,例如 GE Healthcare、GE Aviation、GE Power等也在积极探索这一领域,将 3D 打印融入自己的商业项目。2017 年,通过一系列的技术攻坚和商用转化,GE 进一步巩固了自身增材制造巨头的地位。
(4)德国SLMSolutions
德国 SLM Solutions 集团是世界领先的金属激光增材制造设备生产商及服务提供商,在法克兰福证券交易所上市。一直以来 SLM 专注于选择性激光熔化(SLM)相关的高新技术研发及产业化,致力于提供 3D 金属打印行业最优解决方案。公司同时也是该技术领域的先驱之一,为客户提供具有高自由度形态部件的设计和制造方法,适用于个性化定制及批量生产的部件。公司目前在德国、美国、新加坡、俄罗斯、中国拥有超过 310 名员工。2018 年公司营业收入 7166 万欧元(按照欧元兑人民币汇率 7.86 计算,约合人民币 5.63 亿元),同比下降 13.1%,净利润-1338万欧元。
(5)杭州先临三维
杭州先临三维成立于 2004 年,于 2014 年在股转系统(新三板)上市,2019 年拟在科创板上市。公司总部设在杭州,并在北京、德国斯图加特、美国旧金山等地设有子公司。公司专注 3D 数字化及 3D 打印技术十余年,主营业务为 3D 数字化与3D 打印设备及相关智能软件的研发、生产、销售。公司现已拥有 3D 数字化和 3D打印设备两大核心产品线,为高端制造、精准医疗、定制消费、启智教育等领域用户提供数字化、定制化、智能化的“3D 数字化—智能设计—3D 打印”智能制造解决方案,是拥有自主研发的“从 3D 数字化数据设计到 3D 打印直接制造”的软硬件一体化完整技术链的科技创新企业。公司旗下易加三维专注金属 3D 打印等直接制造 3D 打印技术的研发。公司 2018 年实现营业收入 4.01 亿元,同比增长10.41%;归母净利润 941 万元,同比下降 50.34%;子公司易加三维 2018 年实现营业收入 8655 万元,净利润-5.97 万元。
(6)北京鑫精合
鑫精合激光科技发展(北京)有限公司(以下简称“鑫精合”)以增材制造、特种连接、金属钣金成型、复合材料加工、复杂机械加工、精密装配等先进制造工艺为依托,面向航天、航空、航海、核电等高端制造领域,从事产品设计与优化、原材料制备、结构分总体制造与修复、增材制造设备生产、软件定制开发、技术咨询与服务的国家级高新技术企业;是中国领先的金属增/减材制造技术全套解决方案提供商。2017 年底经过公司资源整合,正式成立精合集团,集团总部位于北京,在天津、重庆、沈阳、西安、潍坊、上海设有分公司/子公司。精合集团掌握国际领先的增材制造技术,其中激光选区熔化(SLM)、激光沉积制造(LDM)等工艺技术具备国际领先水平。公司现拥有 50 台自主研发的系列化金属选区熔化设备,11 台超大型号自主研发的金属沉积制造设备,拥有核心技术专利 100 余项。公司现有在职人员 600 余人,其中技术研发团队 157 人,主要来自于清华、北大、北航、西工大等国家重点高校,以及部分海外人才,团队成员 70%以上拥有 10 年以上的结构产品研制经验。公司依托自身先进制造技术的优势,承接了大量高端制造领域的国家重点型号结构产品的研制生产任务,产品已应用于30 多型飞机、火箭、导弹、卫星、飞船等装备,打破了多项国外技术垄断,填补了国内空白。
(7) 湖南华曙高科
华曙高科成立于 2009 年,是工业级 3D 打印领航企业,拥有高分子复杂结构增材制造国家工程实验室、国际视野的研发体系和全球销售服务网络。公司现有员工超过 280 人,其中研发人员超过 40%,目前共申请专利超过百项,获得专利授权近百项,并先后通过 ISO9001-2008 等质量管理体系认证。2016 年,华曙高科有40%的销售额来自于海外,覆盖 30 多个国家和地区,已逐步建设成为集金属、尼龙 3D 打印设备研发制造,3D 打印材料研发生产以及客户服务支持为一体的全产业链格局。创始人许小曙博士历任美国 3D Systesms 公司 、 Solid s Concepts 公软件开发总监,拥有超过 20 年的增材制造经验,获得过“世界 100 位应用科学领域突出贡献奖”、“最佳人工智能奖”等世界级奖项,曾在全球多家著名增材制造企业领衔关键技术研发及产业化,他研发的 3D 打印设备被誉为“许氏机器”。
四、 趋势
经过 30 多年发展,增材制造产业正从起步迈入成长期,呈现出加速增长的态势。全球增材制造产值从 2012 年的 22.8 亿美元增长到 2017 年的 73.36 亿美元,年复合增长率高达 26.20%。预测,2019 年全球增材制造产值将达到 158 亿美元,2017-2019 年的年复合增长率为 46.72%;2022 年产值将达到 239 亿美元,2019-2022 年的年复合增长率为 14.79%;2024 年产值将达到 356 亿美元,2022-2024 年的年复合增长率为 22.05%。
2012-2024 年增材制造产业及增长率
数据来源:公开资料整理
中国增材制造行业相对欧美国家起步较晚,在经历了初期产业链分离、原材料不成熟、技术标准不统一与不完善及成本昂贵等问题后,当前中国增材制造已日趋成熟,市场呈现快速增长趋势。
在 2015-2017 年的 3 年间,我国增材制造产业规模年均增速超过 30%。2017 年我国增材制造产业规模已超过 100 亿元。初步预计2023 年我国 3D 打印市场规模将达到 110 亿美元左右,年均复合增速超过 37%。
2012-2023 年中国增材制造产业规模及预测
数据来源:公开资料整理
相关报告:智研咨询发布的《2019-2025年中国3D打印机行业市场全景评估及发展趋势预测研究报告》
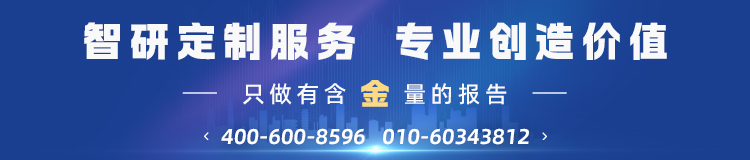
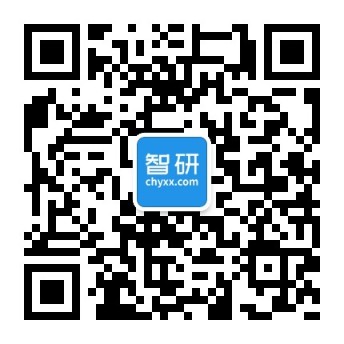
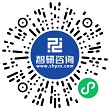
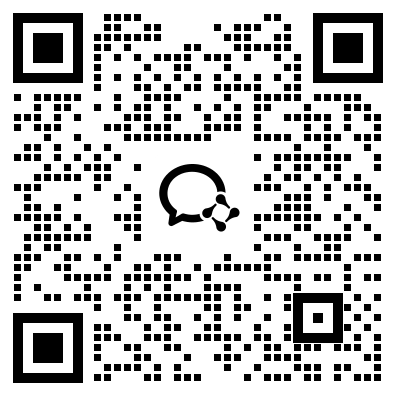